Ajinomoto collaborates with Yusen Food Supply Chain (Thailand) to pioneer the operation of electric trucks for transporting goods, aiming to develop environmentally friendly logistics and promote the society of ‘Eat Well, Live Well’ towards a sustainable future.
For over 60 years, Ajinomoto Co., (Thailand) Ltd., a leading food manufacturer, has initiated its operations in Thailand and continuously grown, expanding its range of food products and services covering both domestic and international markets. Operating under the concept of ‘The Ajinomoto Group Creating Shared Value (ASV),’ which is the core principle guiding its business operations, it aims to balance societal value development and business activities. This concept comprises three main aspects: promoting a healthy society, encouraging the efficient use of resources, and fostering global sustainability.
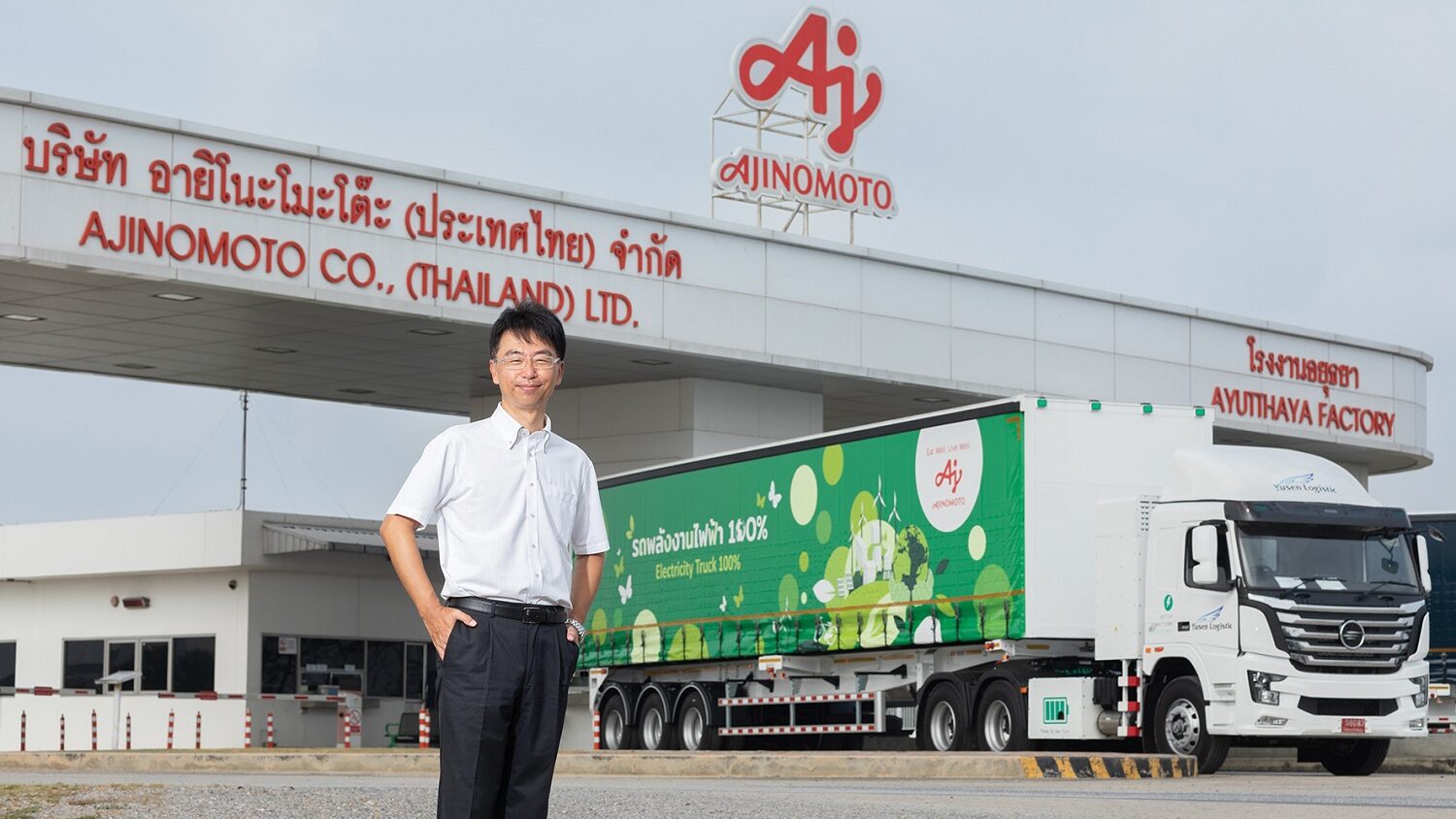
Currently, Ajinomoto is advancing and demonstrating its dedication as a company committed to creating social and environmental well-being. This is achieved by developing environmentally friendly logistics, aiming for a sustainable future. Ajinomoto has initiated using electric trucks for transportation and distribution operations in collaboration with Yusen Food Supply Chain (Thailand), a leading logistics and transportation management company. This official logistics partner of Ajinomoto (Thailand) is responsible for transporting and distributing Ajinomoto’s products. This marks the beginning of implementing transportation practices with zero carbon emissions, driving towards the company’s goal of reducing environmental impact by 50% according to sustainability plans, which will be achieved by 2030.
LM spoke with Mr. Pavin Hutchesson, Associate Director In charge of the Procurement Department and SCM Division at Ajinomoto Co., (Thailand) Ltd., and Mr. Koichi Hirose, Vice President and Chief Operating Officer at Yusen Logistics (Thailand), and President of Yusen Food Supply Chain (Thailand). We discussed the key concepts and collaborative plans between Ajinomoto (Thailand) and Yusen Food Supply Chain regarding the operation of electric truck fleets for transportation and distribution of products within the Ajinomoto group, driving towards carbon reduction in transportation processes.
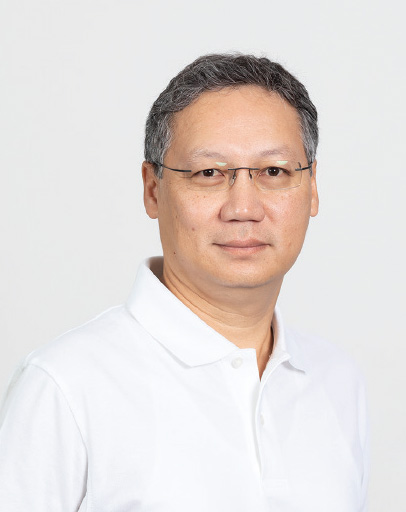
“Ajinomoto has announced its commitment to reducing carbon emissions and efficiently managing Scope 3 greenhouse gas emissions through the use of electric trucks in the distribution and transportation processes of Ajinomoto products, in collaboration with Yusen Food Supply Chain,”
Mr. Pavin Hutchesson, Associate Director In charge of the Procurement Department and SCM Division at Ajinomoto Co., (Thailand) Ltd.,
Empowering a Thriving Community Towards Sustainability
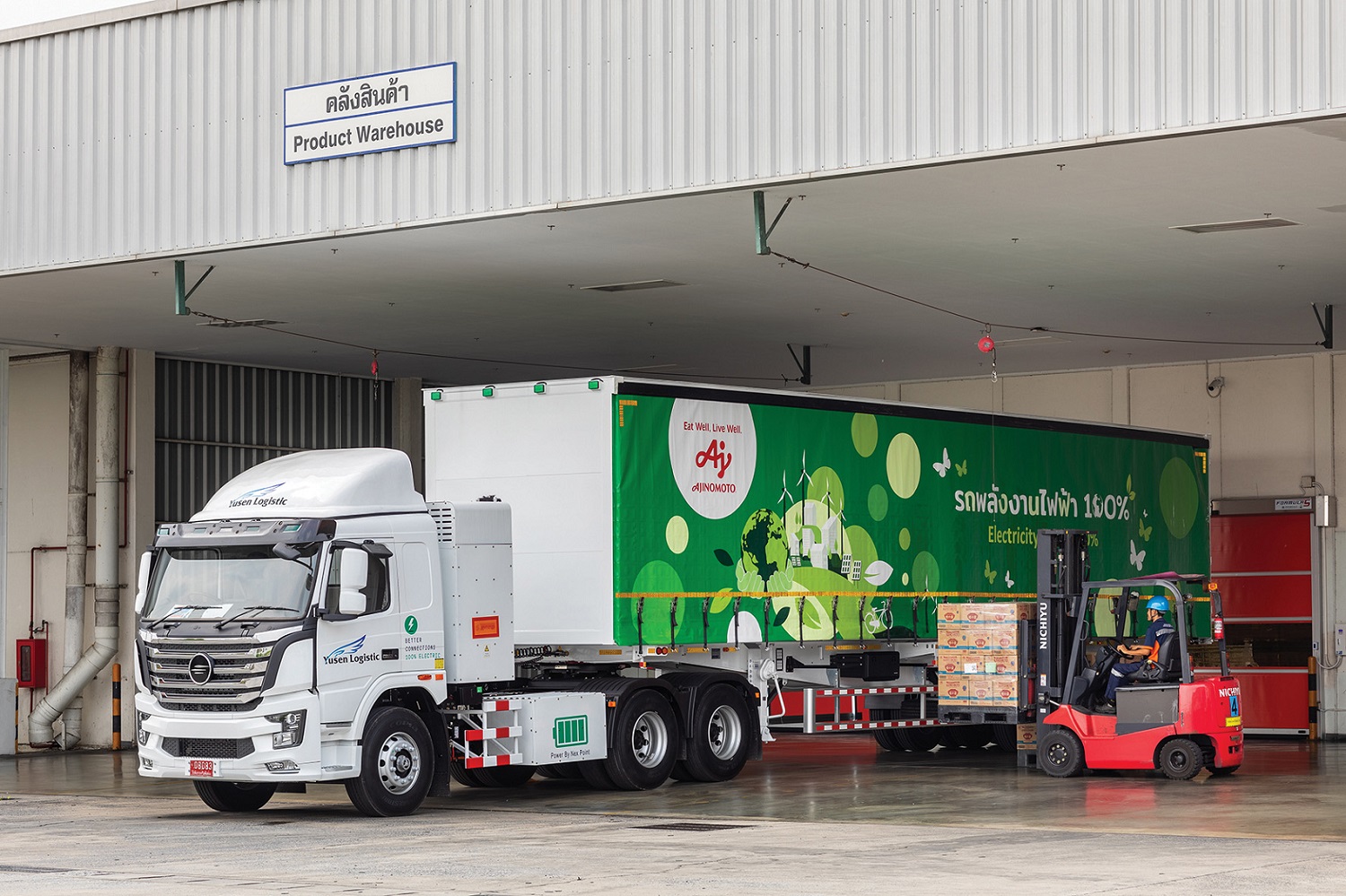
The Ajinomoto Group was established over 110 years ago in Japan with a commitment to contributing to the well-being of people, society, and the world through its products and services. Expanding its business to Thailand in 1960, Ajinomoto (Thailand) was first founded in Phra Pradaeng District, Samut Prakan Province. Initially focused on manufacturing Ajinomoto MSG, the company later diversified its product line to include various food items such as seasonings, instant noodles, ready-to-eat meals, frozen foods, and beverages. Alongside expanding its factories to accommodate the growing business volume, Ajinomoto (Thailand) now operates six factories and four distribution centres throughout Thailand to meet the significant demand for food, which is vital for sustaining people’s lives in society.
The transportation and distribution of goods between factories and distribution centres, as well as commercial centres, are integral activities carried out daily by the company. As a group of companies operating under the ASV (Ajinomoto Shared Value) concept, the aim is to conduct environmentally friendly transportation and logistics operations to reduce carbon dioxide emissions by approximately 50% by 2030. This goal is pursued through collaboration with logistics and transportation service provider Yusen Food Supply Chain (Thailand).
“Established in Thailand for over six decades, Ajinomoto (Thailand) has been transporting products from its factories to distribution centres and customers across Thailand and neighbouring countries every day to support the well-being of people, in line with the slogan ‘Eat Well, Live Well.’ Therefore, Ajinomoto is responsible for developing and creating sustainability for society and the world, emphasizing positive impact creation. Recently, Ajinomoto has announced its commitment to reducing carbon emissions and efficiently managing Scope 3 greenhouse gas emissions through the use of electric trucks in the distribution and transportation processes of Ajinomoto products, in collaboration with Yusen Food Supply Chain,” Mr. Hutchesson stated.
As Ajinomoto remains steadfast in addressing environmental challenges alongside value creation through its business operations, the company places great importance on environmental management and carbon footprint reduction from organizational activities. Ajinomoto (Thailand) has successfully reduced carbon emissions in Scope 1 (direct emissions) and Scope 2 (indirect emissions from energy use) and is actively moving forward to further mitigate environmental impacts in Scope 3, which involves reducing other indirect emissions through collaboration with logistics partners to introduce electric trucks for transportation and distribution operations.
“As electric truck technology and battery capabilities continue to advance, we aim to elevate the usage of electric trucks in Ajinomoto’s entire transportation and distribution operations. Our goal is to transition to 100% electric truck operations for all Ajinomoto transportation and distribution activities.”
Mr. Koichi Hirose, Vice President and Chief Operating Officer at Yusen Logistics (Thailand), and President of Yusen Food Supply Chain (Thailand)
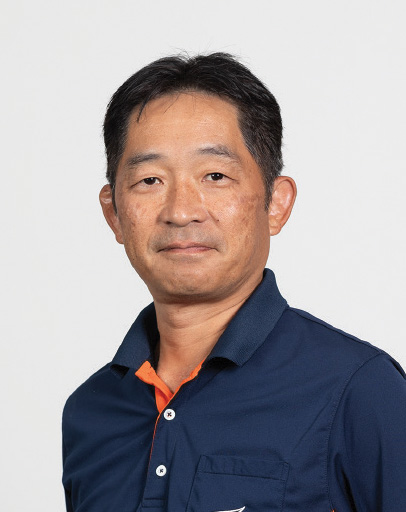
Carbon Emission Reduction Milestones
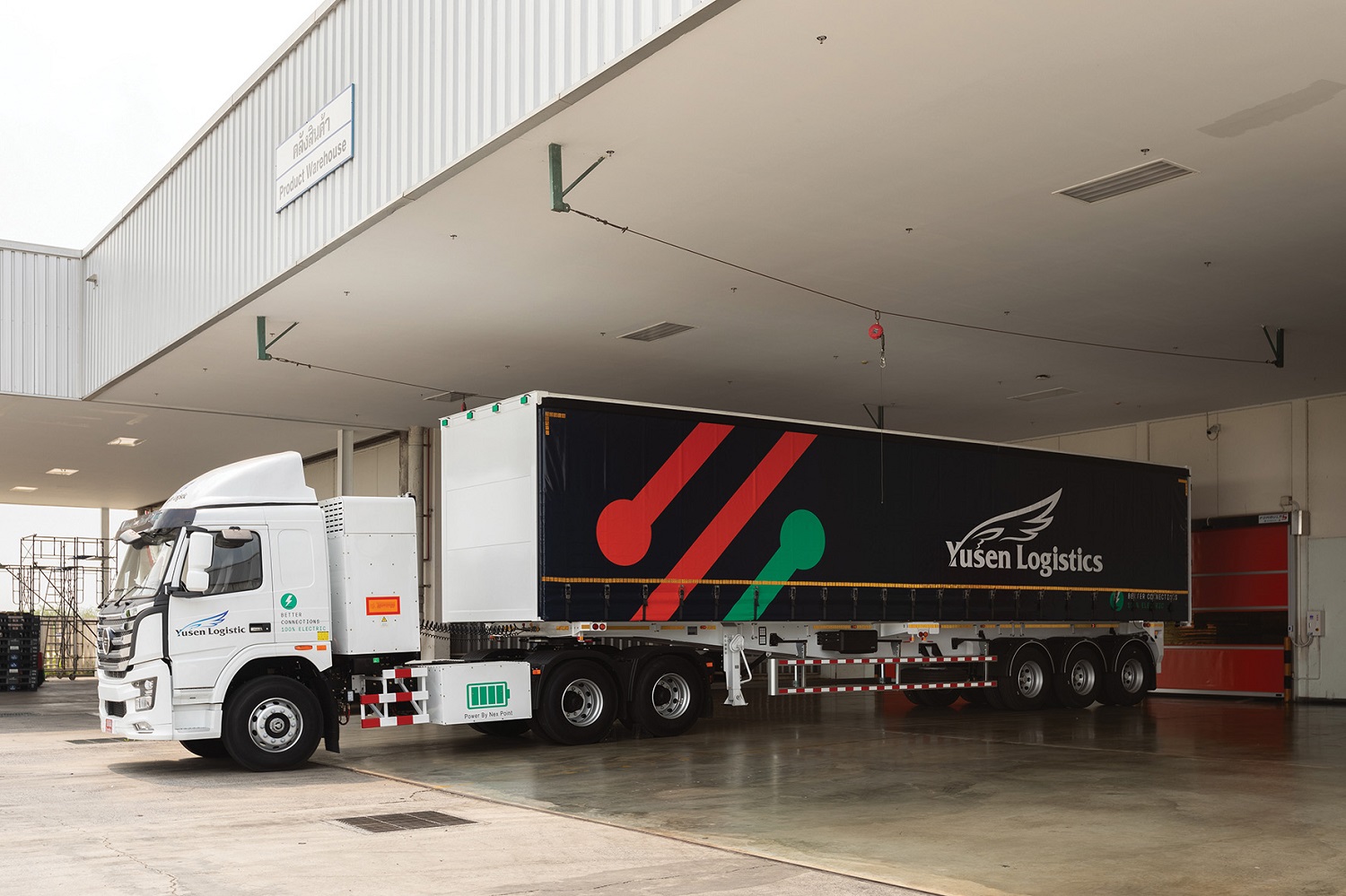
In the strategy for implementing electric trucks, Ajinomoto (Thailand) collaborates with Yusen Food Supply Chain (Thailand), an expert in logistics and food transportation responsible for transporting and distributing Ajinomoto (Thailand) products to distribution centres, customers, and consumers nationwide, including other ASEAN countries. Both companies have planned to enhance environmentally friendly logistics processes, conducted trials, and joined evaluations closely until confidence is gained in adopting electric trucks. Initially, the implementation commences with two 18-wheel electric trucks transporting products between Ajinomoto factories and distribution centres in central Thailand. Subsequently, the number of electric trucks will gradually increase every year. Ajinomoto anticipates that transitioning from conventional diesel trucks to electric trucks will potentially reduce carbon emissions by up to 1,600 tons annually. By 2030, the company aims to achieve a 50% reduction in carbon emissions from Ajinomoto Group activities.
Mr. Hirose commented on this collaboration, stating, “Although electric trucks are still a relatively new technology for Thailand, Yusen Logistics Group has conducted serious testing and operations of electric trucks for transportation. This includes testing operations on various routes, considering costs, feasibility, and environmental pollution reduction. This has led to the adoption of electric trucks for real operations. Additionally, Yusen Logistics has invested in installing charging stations at its operational centers to ensure more flexibility, speed, and seamlessness in operations. Furthermore, we are planning to increase charging stations in other strategic locations in the future.”
Furthermore, Mr. Hirose reinforced the strategic plan by stating, “The initiation of electric truck usage in this collaboration stems from our business approach that prioritizes environmental concerns. Logistics and transportation operations utilizing electric trucks will significantly reduce pollution emissions and promote sustainability. Although current electric trucks can only operate for approximately 300 kilometers on a single charge, as electric truck technology and battery capabilities continue to advance, we aim to elevate the usage of electric trucks in Ajinomoto’s entire transportation and distribution operations. Our goal is to transition to 100% electric truck operations for all Ajinomoto transportation and distribution activities.”
One Vision with Right Partners
Yusen Food Supply Chain, a subsidiary of Yusen Logistics, specializes in the logistics and transportation of food and beverage products. They have an environmentally friendly transportation policy with a vision of connecting people, businesses, and communities through logistics services to create a better future.
“Yusen Food Supply Chain understands Ajinomoto’s plans and requirements very well. Besides their potential to provide logistics services and distribute products nationwide, Yusen Food Supply Chain also has environmental conservation policies and sustainability goals that align with Ajinomoto’s. Both companies recognize that the challenge of reducing pollution emissions in transportation processes requires collaboration. Therefore, we have progressed with a feasibility study plan, summarized the results, and initially decided to use two electric trucks for our product transportation operations. We also plan to increase the number of electric trucks every year gradually.” Said Mr. Hutchesson
For a Brighter Future
Although the initial investment in electric truck operations for this transformation may incur relatively high costs, and the technology may not fully support long-distance transportation yet due to factors such as charging stations and charging time, both Ajinomoto and Yusen Food Supply Chain recognize that addressing environmental and sustainability issues is critically important and urgent. While technology continues to advance, enabling transportation over longer distances, both companies plan to expand their electric truck fleets continuously. They are also preparing to install charging stations at all distribution centres to achieve significant milestones in promoting healthy communities and well-being. They follow Ajinomoto’s vision to be ‘leader in creation of well-being’ and move towards a sustainable and environmentally friendly future.
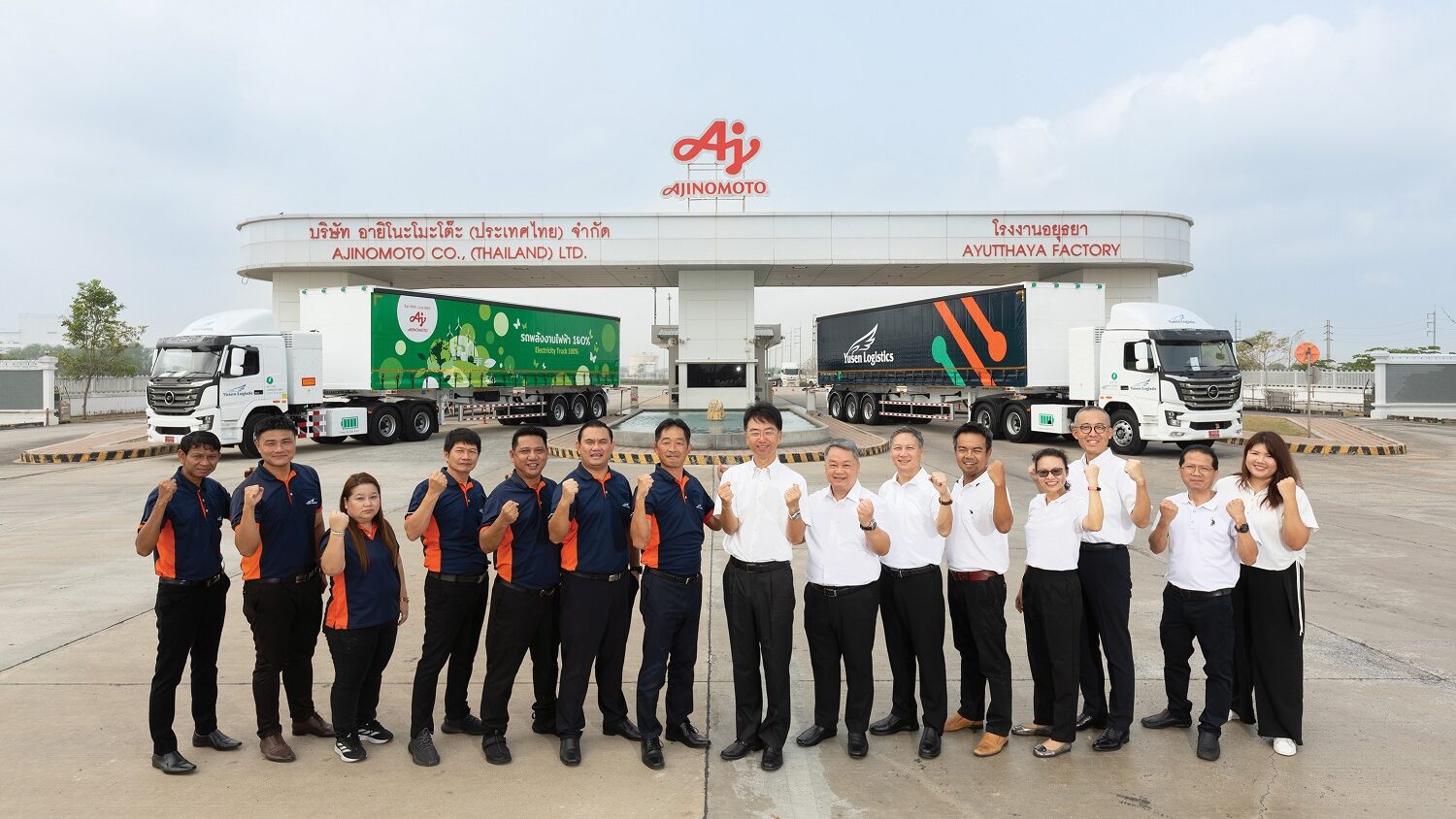
อัพเดตข่าวสารและบทความที่น่าสนใจในอุตสาหกรรมโลจิสติกส์ก่อนใคร ผ่าน Line Official Account @Logistics Mananger เพียงเพิ่มเราเป็นเพื่อน @Logistics Manager หรือคลิกที่นี่